Category: General
Habitat for Humanity ICF Foundation
In the summer of 2022, Habitat for Humanity Door County produced two homes built on I.C.F. Foundations.
Why does this team choose TF System for their foundations nearly every year?
The answer is that TF Systems’ vertical ICF is easy to understand and lightweight; things that matter significantly when you are trying to attract volunteer labor. The organization knows that it doesn’t have to hire expensive foundation installers, or have to buy, maintain, transport and store bulky, heavy, difficult to work with, wood or aluminum forms. TF System is easy to work with and leaves a fantastic R-25 wall when all said and done.
Northeast Wisconsin Foundation – Greenleaf, WI
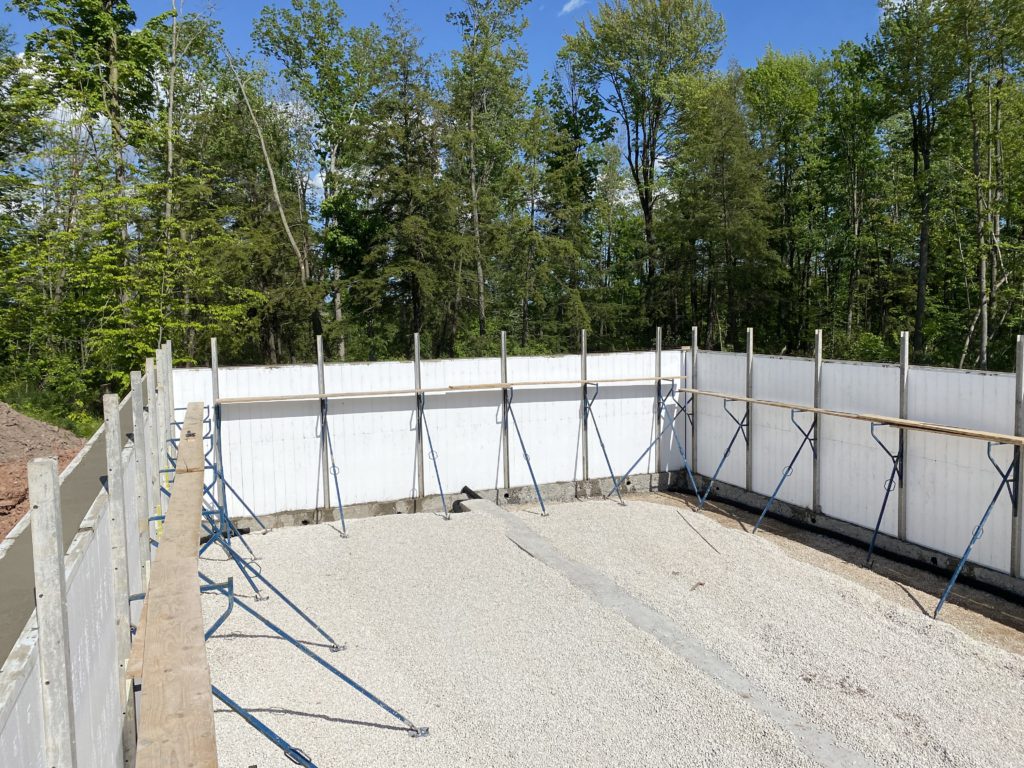
Above is a photo from a new home construction build in 2022. These 10ft. tall walls were erected and poured by a crew the homeowner assembled together along with the help of a company approved independent contractor.
Here is a link to more TF System – the Vertical ICF for the Homeowner looking to build their own foundation
DIY Homebuild in Northeast Wisconsin
TF Forming Systems, Inc. was proud to help with a concrete pour this spring on the second story of a three-story Insulated Concrete Form home build. A father and son (home owner) team constructed the walls, installed the rebar to schedule, and braced the I.C.F. TF Forming Systems, Inc. was there to assist the day of the pour.
Winter Building With ICF
Insulated Concrete Forms are the best way to reduce headaches and stress when trying to get a foundation in before the heavy snow flies and the ground freezes solid. Because of the insulating nature of the 2.5″ polystyrene panels on both sides, the system creates the perfect environment for the concrete chemical reaction to take place even when temperatures dip below freezing at night. This reduces the annoyance of trying to tarp and/or blanket the foundation for days or weeks after the concrete is poured. You can relax knowing that your foundation is as strong and robust as the engineer intended.
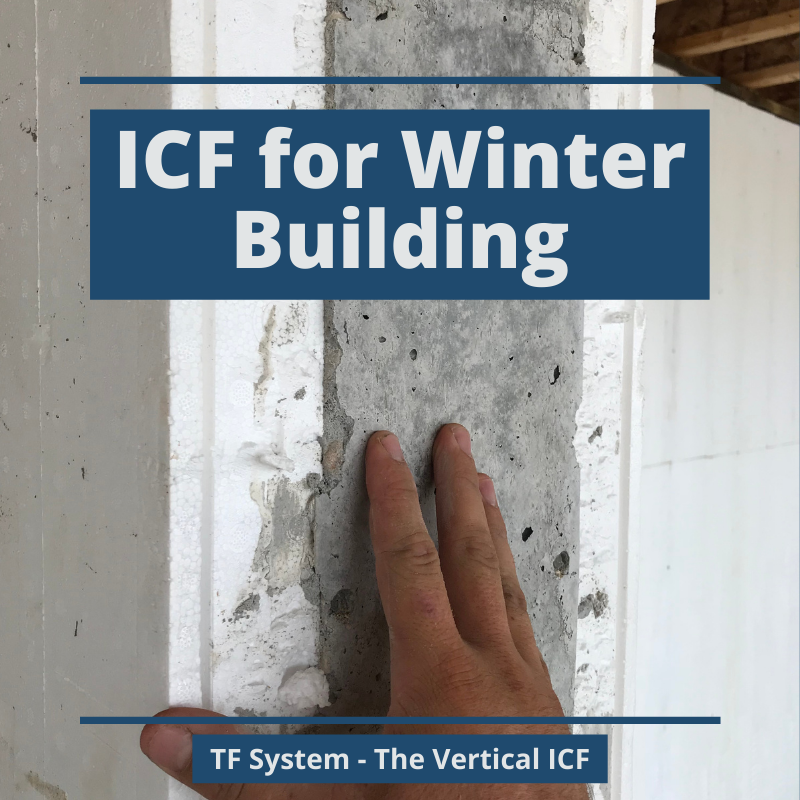
Exemplified in the video below, a DIY homeowner organized this late December concrete pour in Northeastern, WI. Both the conventional retaining walls and the TF System ICF basement walls were poured in the same day; however, only the top portion of the ICF wall needed to be covered and protected by blankets from the cold temperatures at night, whereas the conventional retaining walls needed to be COMPLETELY covered by multiple sets of blankets to keep the concrete from freezing before a full strength cure could be achieved.
World of Concrete 2020
Hey, everyone! We sent the head honcho to World of Concrete 2020 in Las Vegas this year. He sent back some neat videos for us to see and we decided to compile them in a little video for you. Take a look here:
Cutting Splice Pieces
What are splice pieces? What is a more efficient way to cut them?
In the previous blog post, we mentioned how to cut a splice piece, which is a filler piece in a wall where a regular poly panel does not fit. In that post, Jerry Spude demonstrated how to cut a splice piece with a handheld saw, and then he sanded off the rough edges. We also mentioned how you could use a hot wire cutter to cut a splice piece.
In this video, Jerry Spude uses a hot wire table to cleanly and efficiently cut a splice piece. The hot wire table was made on the end of a table saw table for the convenience of adding a groove to the splice piece. In the video, Jerry explains how you can make your own hot wire cutter if this process is something that interests you.
We enjoy using the hot wire cutter in the shop for several reasons:
- Cleanliness
- Efficiency
- Convenience
- Satisfaction of cutting through things with a hot wire
There are more informational “how to” videos on our Youtube page, or check out our manual page for more detailed descriptions of the system.
Splice Pieces
What are they, and how do you cut them?
As Jerry states in the video above, a common question we are asked is “how do you cut our poly panels for a filler piece?” How about what even is a filler piece?
A splice piece, also known as a filler piece, is needed when a vertical wall does not have enough space to fit a full panel but also does not quite reach to the corner. A splice piece is a cut panel piece that can be added anywhere in a wall, middle or end. The video above demonstrates one way to cut a splice piece to fit into your wall.
There are two common ways to cut a splice piece:
- Cordless skill saw
- Hotwire table
There are benefits to using both of these, as demonstrated in other videos. When using a cordless skill saw, it is important to remember to sand off the edge where the saw didn’t completely cut through to have a smooth edge.
Visit our YouTube page for more instructional videos or our manual page for in-depth instructions!
Winter Blues vs Winter Builds
Don’t put your building plans on pause just yet because TF Systems’ Vertical Insulated Concrete System can be used throughout the winter months, even in Wisconsin.
Winter is coming soon, and with it comes snow in the breeze. When that snow hits, people in the North can’t help but think of the impending cold months.
Due to this, many people put plans of building a home on pause come winter months because construction isn’t as feasible. With traditional building methods, this can be true, but with TF Systems’ vertical ICF system, this couldn’t be further from the truth.
How?
To get concrete ready for winter pours, cement is mixed with hot or warm water to reach a temperature of around 70°F. As the cement cures within the insulated walls, it can reach temperatures of up to 130°F. This is because the limestone is curing, burning off the excess water to solidify. The concrete is insulated so it does not settle or shrink in the cold months.
What does this mean for homeowners?
Plans of that dream home, garage, deer stand, cabin, etc. do not have to be put on pause! Homeowners do not have to wait for fair weather to make their dreams come true; they can start at any time of year. Why not cure winter blues by watching your building design come to life? This just means that come the fair-weather months, it’s time to decorate, not build!
What does this mean for contractors?
Bundle up because with these vertical ICF forms, there doesn’t need to be an off season. Building may be cold, especially in Wisconsin, but TF Forming Systems is able to ensure that there can be work available all year long.